History Of Concrete Blocks
Concrete blocks are mainly used as a building material in the construction of walls. Concrete blocks are sometimes referred to as concrete wall block (CMU). Concrete blocks are several precast concrete products used in construction. The term prefabricated refers to the creation and strengthening of blocks before they are brought to the construction site. Concrete blocks also have one or more cavities, and their sides can be flat or patterned. When used, the concrete blocks are laid one by one and held together with fresh concrete mortar to form the desired length and height of the wall.
+90 544 468 75 49


Joseph Aspdin Developed Portland Cement.
Concrete mortar was used by the Romans as early as 200 BC to join the stones formed during the construction of buildings. During the reign of the Roman Emperor Caligula, in 37-41 AD, small precast concrete briquettes were used as building material in the region around present-day Naples, Italy. Concrete technology developed during Roman times was lost after the fall of the Roman Empire in the fifth century. By 1824, English stonemason Joseph Aspdin had developed Portland cement, which became one of the main components of modern concrete.
The first hollow concrete block was created in 1890 in the United States by Mr. Harmon S. It was designed by Mr. Palmer. After 10 years of experience, Palmer received a design patent in 1900. The Palmer blocks were 8 inches (20.3 cm), 10 inches (25.4 cm), and 30 inches (76.2 cm), and their weight was too much. It is known that the production of concrete blocks was carried out by 1,500 companies in the United States in 1905. In the early years, concrete blocks were poured by hand, with an average yield of 10 blocks per person. Currently, the concrete block production technology produces 400 to 2000 concrete briquettes per hour.
+90 544 468 75 49
What Is The Mixture Used In The Production Of Blocks?
The production of concrete blocks includes a mixture of powdered Portland cement, water, sand and gravel. Portland cement produces a light gray block with a fine surface texture and high compressive strength. The concrete block weighs 17.2-19.5 kg. The concrete mix used in the production of blocks and briquettes has a higher percentage of sand and a lower percentage of gravel and water than the concrete mixes used for general construction purposes. This creates a very dry, solid mixture that retains its shape when the briquette is taken out of the mold.
+90 544 468 75 49
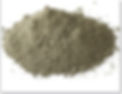

Light Blocks
Light-weight concrete blocks are made using expanded clay or slate instead of sand and gravel. Expanded clay, slate and slate are produced by crushing the raw material and heating it to about 2000 ° F (1093 ° C). At this temperature, the material swells due to rapid gas formation caused by the burning of a small amount of organic material trapped inside. The lightweight concrete block weighs 10.0-12.7 kg and is used for the construction of load-bearing walls. Expanded blast furnace slag, as well as natural volcanic materials, are used for the manufacture of light blocks. The concrete mix used in the production of concrete blocks may also contain various chemicals called additives to change the curing time, increase compressive strength, or increase workability. The mixture may have pigments added to give the blocks color.
+90 544 468 75 49
Block Desing
Widely used sizes and shapes of concrete blocks, standardized to ensure a uniform structure of the building. Conmach Machine, which operates in the Republic of Turkey, also produces moulds for the production of blocks of 8 inches (20 x 20 x 40 cm), 6 inches (15 x 20 x 40 cm), 5 inches (12.5 x 20 x 40 cm), 4 inches (10 x 20 x 40 cm).
Concrete block manufacturers produce specially shaped blocks that have a high level of resistance. Water-repellent additive to reduce the absorption of concrete. Another block design, contains a rough, stony texture on one side of the briquette, rather than a flat surface. This gives the block an architectural appearance of stone that has been cut and chipped.
+90 544 468 75 49


Concrete Blocks Were Used In The Construction Of Buildings.
Concrete blocks were first used in the construction of homes in the United States instead of stone or wood. The oldest known example of a house made entirely of concrete blocks in this country was on Staten Island, New York, in 1837. The houses, built from concrete blocks, showed creative use of common and cheap materials made to look like a more expensive and traditional wood frame stone building. This new type of construction became popular from the early 1900s to the 1920s. The styles of the house, often referred to as "modern" at the time, ranged from Tudor, from Colonial Revival to bungalow. While many homes used concrete blocks and the exterior wall surface as construction, other homes used plaster or other coverings.
Concrete block manufacturers, when designing a new block, must take into account not only the desired shape, but also the production process required to make this shape. Complex moulds or additional steps in the molding process can slow down production and lead to increased costs.
+90 544 468 75 49
How The Production Process Works
The production of concrete blocks consists of four main processes: mixing, forming, curing and cubing. Some machines produces only concrete blocks, while others can produce a wide range of precast concrete products, such as briquettes, hollow blocks, styrofoam blocks, paving stones. The production of blocks varies depending on the model of the concrete blocks making machine, with a capacity of 400 to 2000 per hour of concrete block making machine.
+90 544 468 75 49
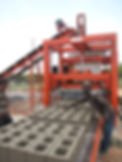

How Is The Production Of Concrete Blocks Carried Out?
-
Mixing
For the production of concrete blocks, sand and gravel are stored in piles outside and transferred to storage bins on site by conveyor belt as needed. The Portland cement is stored outside in large vertical silos to protect it from moisture.
Sand, gravel, and cement are transferred to dispensers that weigh the amount of each material.
The dry ingredients are then placed in a stationary mixer, where they are mixed for a few minutes. There are three types of mixers used in the production of concrete blocks. A planetary mixer is a type of single-shaft mixer used in the production of blocks. The mixer blades are attached to a vertically rotating shaft inside the mixer.
A small amount of water is added to the mixer after mixing the dry ingredients. If the object is located in difficult climatic conditions, the water may first pass through a heater or cooler to regulate its temperature. At this time, chemical additives and coloring pigments can also be added. The concrete is then mixed for six to eight minutes.
-
Moulding Process
The concrete from the mixer is transported to the hopper bucket on the top of the concrete block making machine by a conveyor belt. The moulds consist of two parts, male and female. The moulds define the external mould of the block and the internal mould of the cavities. Up to 15 briquettes can be cast at a time.
When the dies are filled, the concrete is compressed by the weight of the punches, which are lowered onto the die. This compression can be supported by air or hydraulic pressure cylinders acting on the mould head. Concrete block making machine also uses a short burst of mechanical vibration to further aid in compression.
The compressed block is pushed down onto a flat steel pallet and removed from the moulds. Pallets and blocks are pushed out of the machine onto a chain conveyor.
-
Curing
The pallets are transported to an automatic stacker or loader, which places them in the curing area. Each shelf occupies several hundred blocks. When the shelf is full, it is wound on a row of rails and moved to the curing oven.
The furnace is a closed chamber capable of holding several racks at the same time. There are two main types of curing furnaces. The most common type is a low-pressure steam oven. Blocks of this type are left in the oven at room temperature for one to three hours to allow them to harden slightly. The steam is then gradually introduced to raise the temperature at a controlled rate not exceeding 60 ° F per hour (16 ° C per hour). Standard blocks are usually cured at 150-165 ° F (66-74 ° C), while light blocks are cured at 170-185 ° F (77-85 ° C). When the curing temperature is reached, the steam is turned off, allowing the blocks to remain in hot, humid air for 12-18 hours. After soaking, the concrete block is dried by expelling moist air and further increasing the temperature inside the furnace. The entire curing cycle takes about 24 hours.
Another type of furnace is a high-pressure steam furnace, sometimes called an autoclave.
With this type, the temperature rises to 300-375 ° F (149-191 ° C), and the pressure rises to 80-185 psi (5.5-12.8 bar). The blocks are allowed to soak for 5-10 hours. The pressure then quickly discharges, causing the blocks to rapidly release trapped moisture. The autoclave curing process requires more energy and a more expensive furnace, but can dry the blocks in less time.
+90 544 468 75 49
Cubing
The cured block racks are removed from the furnace, and the block pallets are stacked and placed on a chain conveyor. The blocks are pushed out of the steel pallets, and the empty pallets are fed back into the vibrating press.
The blocks pass through a cube that aligns each block, and then stacks them into a three-block cube six blocks deep, three or four blocks high. These cubes are transported to the street by a forklift truck and placed in a warehouse.
+90 544 468 75 49

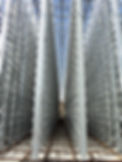
Quality Control
The production of concrete blocks requires constant monitoring for production with the necessary properties. The raw material is weighed before being placed in the mixer. The water content can be measured by sensors, and the amount that will be added to the mixture is automatically adjusted. In areas with a special climate, the water may be cooled or heated before use.
When the blocks come out on the vibropress, their height can be controlled using laser sensors. In the furnace, the temperature, pressure, and cycle time are automatically monitored and recorded to ensure that the briquettes are properly cured to achieve the required strength
+90 544 468 75 49
The Future
The production of concrete blocks will be improved in different shapes and sizes with new projects created by architects, engineers, and block manufacturers. By giving structures a visual feature, the blocks promise to make building construction faster and cheaper, as well as get stronger and more energy-efficient structures. Some of the possible concrete block designs for the future include a bi-axial block with gaps that extend horizontally and vertically to allow access to plumbing and electrical pipes; a stacked facing block consisting of three parts that make up both the interior and exterior walls.
+90 544 468 75 49
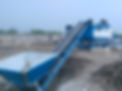